1. Tourniquets for the Ukraine Conflict
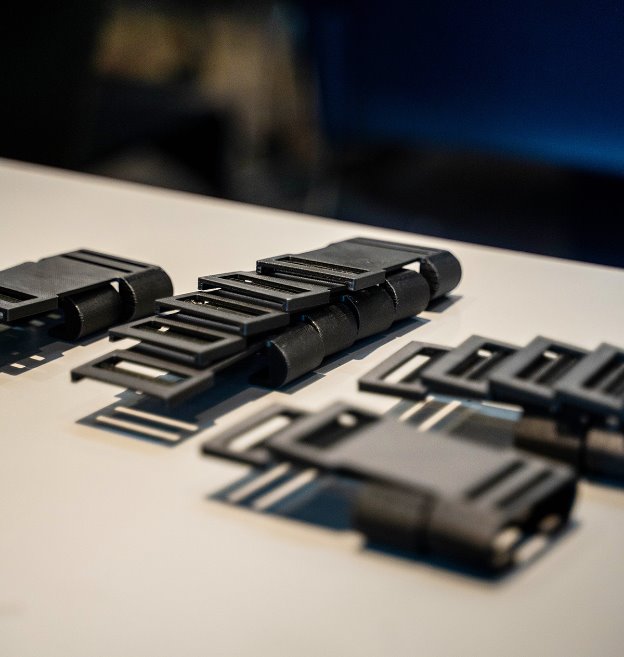
Project DIAMOnD Member:
Ultimation Industries, LLC
Roseville, Michigan
“As a manufacturer, Project DIAMOnD has allowed us to experiment with 3D printing and innovate for our own business while simultaneously giving us the opportunity to aid in humanitarian efforts when called upon. It’s a win-win.”
- Richard Canny, President
- Project DIAMOnD participants produce tourniquet clips in response to a request from the Ukrainian Defense Ministry.
- Proved the real-world scalability, agility, and impact of distributed manufacturing.
2. Innovative Tooling for Mold Injection Machine Shop
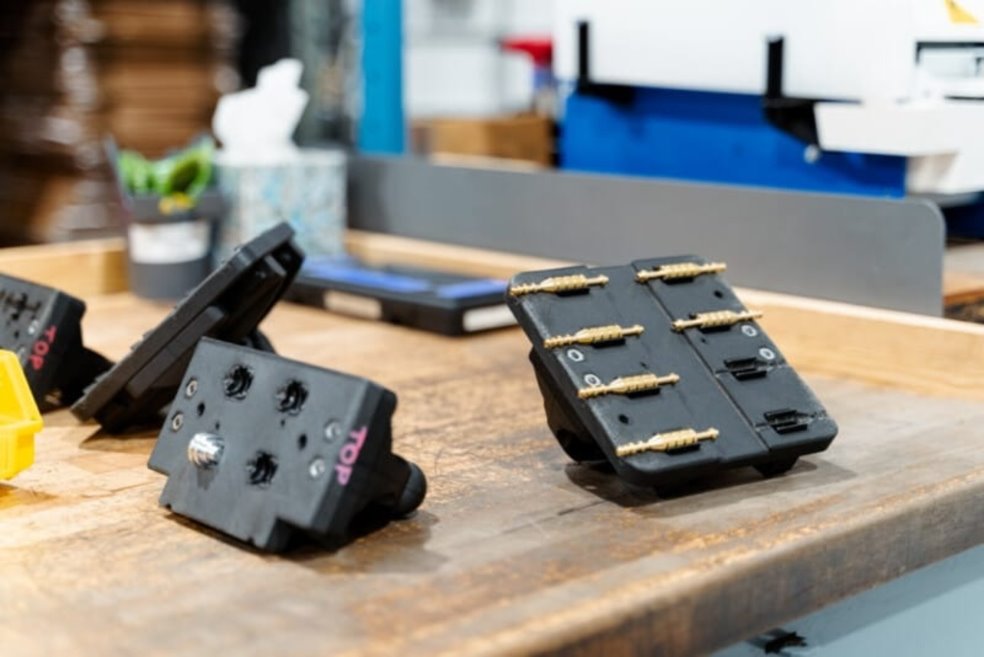
Project DIAMOnD Member:
Zero Tolerance, LLC
Clinton Township, Michigan
“I did not believe that we could print real tools that would work on the shop floor like this does. 2020 changed our plans and budget for this end-of-arm tooling and robot. The robot was no longer an investment that could be justified as volumes dropped in 2020. Now, we have a solution that will give us the ability to increase our capacity with very little cost and the option to build a version that will work with a robot when the time comes.”
– Steve Michon, President
- Zero Tolerance LLC, a plastic mold injection machine shop, leveraged its Project DIAMOnD 3D printer to develop a hand-held, multi-part insert tool called “The Claw.”
- Originally planned as an aluminum part, the company opted for a 3D-printed solution that increased efficiency and reduced costs on the shop floor.
- Enabled cost-effective production while maintaining flexibility for future automation integration.
3. Turning a $100 Part into a $1 Part for an Industrial Equipment Supplier
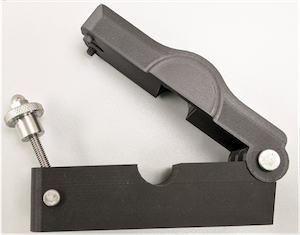
Project DIAMOnD Member:
Air & Liquid Systems
Rochester Hills, Michigan
- Air & Liquid Systems leveraged its Project DIAMOnD 3D printer to replace a $100 stainless steel part with a $1 carbon fiber version, achieving a 99% cost reduction.
- The printer is strategically placed in the engineering area to spark innovation and curiosity, encouraging engineers to rethink traditional production methods.
- The initiative is shifting the company’s mindset, fostering a culture of continuous improvement and digital transformation.
- Positions Air & Liquid Systems for long-term gains in Industry 4.0 adoption, demonstrating the real-world impact of additive manufacturing on efficiency and business strategy.
4. Overcoming Pandemic Supply Chain Issues
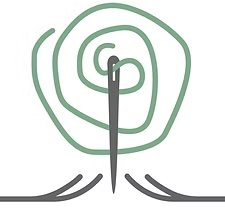
Project DIAMOnD Member:
Unique Short Tree
Rochester Hills, Michigan
- Unique Short Tree, a restoration and upholstery business, turned to 3D printing during the pandemic to overcome supply chain disruptions that made key parts unavailable.
- Through Project DIAMOnD, the company designed and 3D printed critical components, describing the technology as a savior in keeping operations running.
- Previously inexperienced with 3D printing, the company now plans to continue using it due to cost savings and production efficiency.
- Looking ahead, Unique Short Tree plans to offer 3D printing services to customers, expanding its business model.
5. Durable Parts Withstanding Heat and Tension
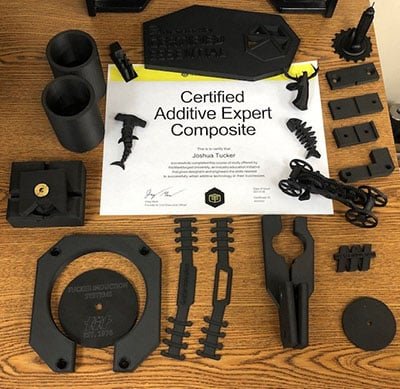
Project DIAMOnD Member:
Tucker Induction System
Shelby Township, Michigan
“This technology is not just for prototyping. You can actually print parts and put them out in the field.”
– Josh Tucker, Tucker Induction System
- Tucker Induction System leveraged Project DIAMOnD 3D printing to produce durable, real-world parts that can withstand tension, heat, and other forces.
- The company replaced subtractive manufacturing methods with 3D printing for certain parts, reducing costs and production time.
- Beyond replacing parts, 3D printing is now being used to develop completely new solutions, expanding innovation opportunities.
- Demonstrated that additive manufacturing is viable for functional, end-use parts, not just prototyping.
6. Inspection Fixtures Made Easy with 3D Printing
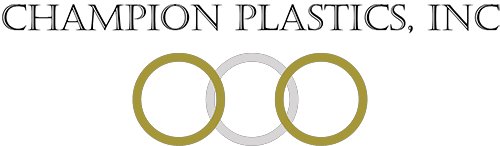
Project DIAMOnD Member:
Champion Plastics
Auburn Hills, Michigan
“Project DIAMOnD has allowed Champion Plastics to add a new element to our capabilities where we utilize the 3D printer to create custom inspection fixtures for our injection molded parts. In the past, we relied on custom CNC’d aluminum fixtures which took time and were costly. Combined with the Project DIAMOnD CAD design training and the supplied 3D printer, we now have this capability in-house at a fraction of the cost and time.”
– Jeff Ignatowski, President
- Champion Plastics integrated Project DIAMOnD 3D printing into its quality inspection process, creating custom fixtures for injection-molded parts.
- Previously, the company relied on CNC-machined aluminum fixtures, which were more expensive and time-consuming to produce.
- With Project DIAMOnD’s CAD training and 3D printer, the company can now design and print fixtures in-house, significantly reducing costs and lead times.
- Demonstrated the impact of 3D printing in improving efficiency, flexibility, and cost savings in manufacturing operations.
7. Reshoring the Supply Chain for The Moon Ring
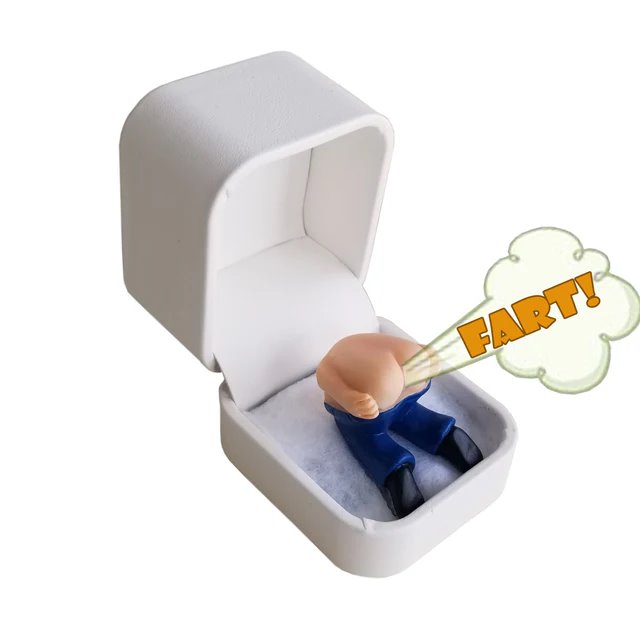
Project DIAMOnD Member:
The Moon Ring
Rochester Hills, Michigan
- The Moon Ring, a popular novelty product featured on The Bachelorette in 2020, previously spent $10,000-$15,000 annually importing plastic parts from overseas.
- Sourcing these parts was challenging, costly, and often resulted in poor-quality components that were unusable.
- Through Project DIAMOnD, owners Eddie and Alison Moffett received a grant-funded 3D printer, training, and consultation, allowing them to 3D print parts in-house with perfect results every time.
- This shift eliminated overseas sourcing challenges, reduced costs, improved quality control, and kept production in the USA.
- Demonstrated how 3D printing technology can empower small businesses to increase efficiency, reduce supply chain risks, and remain competitive.